oder: Warum es schwierig ist, einen gut funktionierenden Delta zu bauen…
Dieser Artikel behandelt im wesentlichen die Hardware. Ein Artikel zur Software bzw. zum Drucken selbst kommt dann ggf. später noch mal. Alles auf einmal würde den Rahmen dieses sowieso schon sehr langen Artikels sprengen.
Vorwort
Ich nehme einfach mal an, Du hast diese Seite gefunden, weil Du drauf und dran (oder dabei) bist, dir einen (Delta-)3D-Drucker selber zu bauen. Vorab: davon will ich niemanden abhalten, das macht viel Spass, man lernt viel und sammelt Erfahrungen in verschiedenen Disziplinen, ich will hier nur aufzeigen, was so meine Erfahrungen mit 3d-Druckern, und Delta Printern im Besonderen sind, und wo etwaige Fallstricke sind.
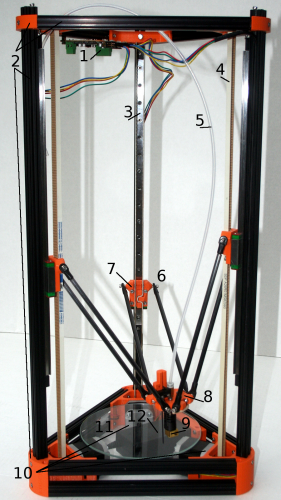
1 Elektronik, z.B. Arduino mit Ramps
2 Rahmen aus Aluprofilen und gedruckten Ecken
3 Linearschienen aus gehärtetem Stahl
4 GT2-Riemen für die Vertikalwagen
5 Bowden-Schlauch mit Hotend und Extruder(nicht im Bild) verbunden
6 Platform-Arme
7 Wagen mit Riemenbefestigung
8 Platform
9 Hotend (hier: J-Head)
10 Motoren
11 Druckbett mit Heatbed oder Glasplatte
12 Netzteil
Quelle des Originalbildes:
http://reprap.org/wiki/File:Kossel.jpg
Lizenz: GNU-FDL 1.2
Einleitung
Ich habe gut ein Jahr lang mit dem 3D-Drucker eines Freundes Erfahrungen gesammelt (was 3D-Druck an und für sich und die Bedienung von Drucker und Software angeht), bevor wir uns entschieden, für unseren Hackerspace auch einen Drucker zu bauen, und natürlich auch gleich Einen für Zuhause. 2012/13 waren Delta-Printer nun mal das hippeste wo gab, also sollte es ein Delta werden, wo wir auch schon bei den ersten beiden „Lessons learned“ wären (ich fasse die am Ende noch mal zusammen):
Lesson 1: Der erste Drucker den man baut, sollte ein Einfacher sein. Die meisten Teile sind eh wieder benutzbar, man braucht also mitnichten alles neukaufen, wenn man sich später für was Anderes entscheidet. Zugegebenermaßen waren die ersten beiden Drucker die ich gebaut habe eben diese beiden Deltas, aber zum einen hatte ich schon viel Erfahrung mit 3D-Druckern und zum zweiten bin ich dann am Schluss doch noch mal gelernter Schlosser, dessen Betätigungsfeld nicht unbedingt war, den ganzen Tag den großen Hammer zu schwingen, sondern durchaus komplexere Geräte ausseinander und zusammen zu bauen als 3D-Drucker. Dennoch würde ich es heute als Fehler bezeichnen, direkt mit Deltas angefangen zu haben.
Lesson 2: Gigantismus bei Deltas geht entweder mit Mehraufwand oder Qualitätseinbußen daher (oder beides). Dazu vielleicht ein paar erklärende Worte im nächsten Abschnitt.
Mechanischer Aufbau
Gigantismus… ein großes Problem sich dem zu entziehen, wenn man einen Delta bauen will. Die Gedankengänge sind normalerweise etwa wie folgt: „Diese ganzen Drucker die ich bis jetzt gesehen habe, sind ja ganz nett, aber irgendwie wäre es ja toll, wenn man auch hohe Sachen drucken könnte, nen halber Meter oder mehr sollte bei diesen Delta Dingern doch kein Problem sein … (Druckhöhe, nicht Höhe des Druckers selbst.)“.
An dieser Stelle sei gesagt: Ja, das ist tatsächlich kein Problem, hohe Sachen kann man in der Tat gut mit Deltas drucken, ABER ein sehr hoher Drucker (sagen wir mal alles über 600mm Gerätehöhe) stellt besondere Anforderungen an den mechanischen Aufbau des Druckers. Die Standard 20x20mm oder gar 15x15mm Aluprofile mit gedruckten Ecken, der über nicht ordentlich gefluchtete Ritzel und Umlenkrollen den GT2-Zahnriemen schräg durch die Gegend zieht, kann bei einem relativ kompakten Format eines „Kossel Mini“ vielleicht noch funktionieren, aber je größer der Drucker wird, desto sorgfältiger muss man arbeiten, und im Zweifel bessere (und damit deutlich teurere) Materialien benutzen. Je weiter man sich vom „Standard“-Formfaktor eines Kossel Mini entfernt, desto schwieriger wird es, von der Stange Teile zu kriegen, aus denen man sich einen Drucker bauen kann, zumindest bezogen auf Deltas.
Darum Lesson 3: Nahe am „Standard“-Kossel zu bleiben, erspart viel Arbeit.
Natürlich will ich niemanden davon abhalten, einen großen Drucker zu bauen, aber man sollte sich im Hinterkopf behalten, dass alles sehr viel komplizierter wird, wenn man groß baut, und für jemanden, der nicht viel Erfahrung im „Schrauben“ hat, und im Zweifel nicht weiß, wie man entsprechend improvisiert, für Den ist das nichts. Ausnahmen bestätigen hier natürlich auch hier die Regel, aber in der Regel endet das eher in Frust. Nicht nur dass sich Toleranzen beim Aufbau eher exponential denn linear auswirken, je größer man wird, stellt man schnell fest, dass
- man keine passenden Druckbetten kriegt für seine Größe (sowieso ein Problem bei Deltas), von Druckbettbeschichtung jedlicher Art mal ganz abgesehen,
- die Motoren auf einmal für die Größe zu schwach sind, und man an seine Elektronik jetzt wirgendwie extern die größeren Treiber anflanschen muss
- das Hotend nur Fäden zieht, obwohl der Retract schon bei >=5mm steht, einfach weil der Bowdenschlauch so lang sein muss bei dem Aufbau
- und zu allem Überfluss der ganze Aufbau trotz leichter Center-Platform wackelt wie der Hinterteil eines Dackels beim Drucken,
- die große Größe Instabilität bei gleichbleibender Materialstärke zur Folge hat.
Gute Gründe bei moderaten Druckergröße zu bleiben
Erprobt. Den meisten wird es darum gehen, einen 3D-Drucker zu bauen, den man benutzt, hin und wieder was dran bastelt, und dabei noch fancy und hypnotisierend aussieht wenn man ihm beim Arbeiten zusieht, nicht aber irgendeine Machbarkeitsstudie zu verifizieren. Insofern ist es keine Schande auf ein gut erprobtes Konzept und Design zu setzen, auch wenn es einen nachvollziehbarerweise in den Fingern juckt, ein absolutes Unikat auf dem Schreibtisch stehen zu haben.
Beschaffbarkeit von Teilen. Die mit Abstand meisten Teile bei 3D-Druckern sind einfach beschaffbar und komplett austauschbar. Mit den Delta-Druckern verhält sich das wegen dem dreieckigen Aufbau durchaus etwas anders. Viele Teile kriegt man einfach nicht im „Pack of 3 Pieces“, und grade was das Druckbett sowie dessen Befestigung angeht, wirds bei Deltas echt spannend, gefühlt muss an jeder Stelle das Rad neu erfinden, was sinnvollen Aufbau und Befestigungen angeht. Zugegeben, in den letzten 2-3 Jahren hat sich die Situation doch deutlich verbessert, was die Verfügbarkeit von Teilen angeht, unterdessen kriegt man sogar Kossel-Rahmen-Ecken aus Aluminium, aber dennoch: Es ist nicht so einfach wie es den Anschein macht. Auch die Befestigung des Hotends sowie etwaiger Lüfter an der hängenden Platform kann mitunter schwierig werden, wenn man nicht grade ein default J-Head (oder kompatible, wie E3D) hat, und hier sollte man die Hotends nicht unterschätzen, grade bei J-Heads (die ich zwar generell nicht empfehle, aber das ist ein anderes Thema) kommt es bei mangelnder Kühlung des PEEK-Teils des Hotends dazu, dass eure (im Zweifel gar aus PLA gedruckte, weil die meisten Deltas nur PLA drucken) Hotendaufnahme, bzw. die ganze Platform einfach mal nach unten durchsackt, weil sie im Begriff ist zu schmelzen (bei völlig normalen ~200-225°C Hotend-Temperatur wohlgemerkt), und ihr euch wundert, warum euer Nullpunkt jedes Mal wieder nicht stimmt, weil das Hotend jedes Mal beim Warmwerden durchsackt, und beim Erstarren wieder sich etwas nach oben zieht. Nicht zuletzt bekommt man bei Bedarf auch komplette Kits für Kossel-Minis, wenn man dass denn möchte.
Stabilität. Ein Drucker von der Größe eines Kossel Mini mit 20x20mm-Alu-T-Profilen (statt mit normal 15x15mm Profilen) ist unglaublich stabil und verwindungssteif. Einer, der einen Meter hoch ist und >300mm lange Seitenprofile hat, wackelt wie nichts Gutes beim Drucken. Grade dieser Punkt wird glaube ich bei Deltas am meisten unterschätzt. Da einer der grundsätzlichen Vorteile von Deltas darin liegt, schnell drucken zu können, da die bewegten Teile (also die „Platform“) relativ leicht sind, sind relativ hohe Verfahrgeschwindigkeiten erreichbar, allerdings gibts es auch dazu eine Kleinigkeit zu beachten:
Lesson 4: Verfahrgeschwindigkeit != Bewegungsgeschwindigkeit !
Mal angenommen euer Verfahrsystem ist in der Lage, Geschwindigkeiten >= 300mm/s zu erreichen, bedeutet das jedoch nicht, dass ihr im Slic3r oder welchem Slicer auch immer bei „Travel Speed“ einfach 300mm/s eintragen könnt, denn der Speed bezieht sich darauf, in welcher Zeit sich das Hotend bzw. die Platform von A nach B bewegt, nicht wie schnell sich die Motoren bewegen, oder wie schnell sich ein Schlitten über eine Schiene bewegt. Davon hat eure Drucker-Firmware oder euer Host-Programm wie bspw. RepetierHost keine Vorstellung. Dazu zwei einfache Beispiele, die das verdeutlichen sollen:
- Ihr benutzt einen „geared Wade-Extruder“ (sowas hier), der mit Ritzeln eine Übersetztung macht, der Extruder-Motor bewegt sich also schneller, als wenn er direkt das Filament schieben würde, braucht dafür aber auch weniger Kraft. Dieses Beispiel betrifft natürlich nicht nur Deltas.
- Euer Hotend bewegt sich von Position X-50 Y-50 Z1 nach X50 Y-50 Z1, also von vorne links nach vorne rechts, einen Millimeter über dem Druckett. Während sich der hintere (Z) Motor so gut wie gar nicht bewegt, bewegen sich die X und Y Motoren mit nahezu doppelter Verfahrgeschwindigkeit auf bzw. ab. Bei Deltas ist das normal, da bei nahezu jeder Bewegung alle 3 Motoren bewegt werden, und der einzige Fall, wo Verfahrgeschwindigkeit des Hotends und die Bewegungsgeschwindigkeit der Mechanik gleich ist, ist wenn NUR Z, also in der Höhe verfahren wird, weil sich dann alle Motoren gleich auf oder ab bewegen. Das ist wohl der größte Unterschied zwischen Deltas und „normalen“ karthesischen Druckerprinzipien (mit Ausnahme von Core-XY-Druckern, aber das ist ein anderes Thema) was die Bewegungslogik angeht.
Druckbett
Das Druckbett bei Deltas stellt eine besondere Herausforderung dar. Zum einen ist ein rundes Bett zu empfehlen, was aber ein paar Problemchen mit sich bringt, z.B. wenn der Durchmesser nicht genau zu der Kantenlänge des Druckers passt, kann es schon mal eng werden. Man kann theoretisch auch ein normales, quadratisches PCB-Bett nehmen, allerdings muss man dann mit Aluschienen o.Ä. das erst mal auf den Rahmen bringen, weils sonst nicht passt. Einfacher ist es definitiv mit einem Runden Bett.
Absolut nicht empfehlenswert sind meiner Meinung nach die so hoch gelobten „Bor-Silikat-Glasscheiben“. Das Hauptproblem hier ist wie so oft, dass jemand ein Proof-of-Concept Drucker baut, wie z.B. bei den Deltas Johann Rochol, auf den ursprünglich der Kossel und der Rostock zurückgehen, und der auch viel Code zu Drucker-Firmwares beigetragen hat, damit Deltas damit ordentlich funktionieren. Allerdings wollen(?) viele Andere, die das Nachbauen, offenbar nicht einzelne, konstruktive Entscheidungen hinterfragen, die evtl. aus Design-Gründen getroffen wurden, oder um die Nachbau-Komplexität (im Sinne von „Anzahl der Teile“) zu verringern oder weil es als ShowCase-Effekt was hermacht, wenn man einfach auf eine runde Glaspatte druckt, oder einfach weil besser aussieht in den Augen des Konstrukteurs, oder oder oder… dafür aber unter Umständen ein sehr viel sorfältigeres Arbeiten erfordern beim Aufbau. Man sollte sich nicht nur Gedanken über den eigenen Skill-Level machen beim bauen, sondern hin und wieder einzelne Aspekte hinterfragen, wenn man Drucker nachbaut. Oft kommt man auf Lösungen, die für einen persönlich viel besser funktionieren.
Lesson 5: Auch beim Nachbau konstruktive Entscheidungen hinterfragen!
Ich will nicht sagen, dass es nicht funktioniert, auf eine runde, unbeheizte Glasplatte zu drucken, das tut es sehr wohl, aber es ist in meinen Augen unverhältnismäßig viel Aufwand, denn damit Das ordentlich funktioniert, muss alles passen, alles genau Verfahren, der Abstand zum Druckbett minutiös eingestellt (und am besten mit Messuhr eingerichtet) sein. Natürlich ist es immer besser, wenn alles so genau kalibriert ist, wie möglich, aber bei einer unbeheizten, fest montierten Glasscheibe ist es eine Grundvorraussetzung, dass alles gut bis sehr gut kallibriert ist, damit man überhaupt zu brauchbaren Ergebnissen kommt.
Darüber hinaus liest man häufig, dass „levelbare“ Druckbetten, will meinen „auf Federn gelagerte, mittels Schrauben in der Höhe einstellbare Druckbetten“ bei Deltas überflüssig seien. Das sehe ich Grundsätzlich anders, aus mehreren Gründen.
- Es kann zuweilen schwierig sein, ein Druckbett wirklich „eben“ zu befestigen, eine halbe Umdrehung zu viel oder zu wenig an irgendeiner Schraube, und schon stimmts nicht ganz, obwohl das Bett „fest“ ist; ein wenig fester, und das Druckbett verzieht sich allein durch das Verschrauben/Verklemmen (ok, vielleicht nicht so stark bei Glas, aber bei allen anderen Druckbetten doch deutlich genug).
- Zweiter und wichtigster Grund ist wohl, dass es in unserer unperfekten Welt einfach vorkommt, dass starke Überhänge beim Drucken dazu neigen, sich nach oben zu „wellen“, besonders bei PLA. Auch „Wände“ die so dünn sind, dass sie nur eine einzelne Bahn Plastik (Perimeter) als Füllung haben, kriegen da schon mal zu viel Material ab, dass sich dann etwas nach oben ausdehnt. Das hat zur Folge, das der Drucker über solche Stellen bei „Travel Moves“, also schnellen Bewegungen von A nach B, um die Position zu wechseln mit dem Hotend über solche Stellen drüberscheppert, und zwar mit hoher Geschwindigkeit. Selbst wenn man z.B. bei „Lift Z“ im Slic3r großzügige Werte eingestellt hat, wird man dieses Problem nicht ganz los. Man muss nicht lange nachdenken, um zu erkennen, dass sowas zum einen für das Hotend selbst nicht gut ist, und zum anderen dazu führen kann, dass sich Teile am Drucker verziehen und damit eine erneute Kalibrierung nötig machen, oder dass sich durch die hohe Aufschlagenergie Teile mit geringer Auflagefläche zum Bett lösen können während des Drucks, was immer sehr schlecht ist. Ein gefedertes Bett drückt sich in solchen Situationen nach unten weg . Damit sind die eigentlichen Probleme daran zwar nicht gelöst, dennoch kann man die Sache damit deutlich entschärfen, grade was die Gefahr der Beschädigung des Hotends angeht.
Daher Lesson6: Ein rundes Alu-PCB-Druckbett auf Federn ist besser als eine fest montierte Bor-Silikat-Scheibe.
Auch beim Punkt „beheiztes Bett – ja oder nein“ scheiden sich die Geister. Ich persönlich bevorzuge ein beheiztes Druckbett. Zwar steigt dadruch die Komplexität des Druckers, ebenso wie der Strombedarf, die Druckzeit und die Dimensionierung des Netzteils, aber ein warmes Bett mit geeigneter Oberfläche (Pei beschichtet, Kapton, Haarspray, BuildTak, you name it..) sorgt einfach für signifikant bessere Haftung. Ausserdem hält man sich die Option offen, mit ABS und anderen Kunststoffen zu drucken, die ein beheiztes Bett unabdingbar machen.
Antriebssystem
Gleich mehrere Systeme sind hier möglich. man sollte sich früh entscheiden, auf welches Prinzip man setzen will, denn diese Entscheidung hat wohl die größten Auswirkungen darauf, wie der Drucker hinterher aussieht und welche Teile man benötigt. Im folgenden will ich versuchen, die Vor- und Nachteile der verschiedenen Systeme gegenüber zu stellen.
Antriebssysteme
Prinzip | Vorteile | Nachteile |
---|---|---|
Lager auf Wellen, Subtypen: * Linearkugellager, * linuearkunststofflager (IGUS) | Sehr günstig. Kunststoffausführung sehr spielarm und quasi wartungsfrei. | Ungenau und zu flexibel wenn zu lang, Schlechte Befestigungsmöglichkeiten, Weniger Geschwindigkeit, wenn schlecht geschliffen oder beschädigt. |
Linearführungsschienen mit Wagen,, Subtypen: * Komplett aus Metall * Teilweise aus Kunststoff (IGUS) | Präzise. Leise. Hohe Geschwindigkeit. Hohe Beschleunigung. | Sehr teuer. Qualität vom Preis abhängig. Wagen darf nicht von Schiene rutschen! |
Fishing Line | Leise. Relativ Platzsparend. Notwendige Mechanik ist druckbar. | Keine großen Kräfte möglich. Weniger Beschleunigung. Weniger Geschwindigkeit. Eher Proof of Concept. |
V-Slot | Einfach. Günstig. Teilw. druckbar | Hoher Platzbedarf. Durchrutschen möglich. Weniger Möglichkeit Kabel zu verlegen. Hoher Verschleiß und Wartungsaufwand. Spannung/Spiel muss häufiger korrigiert werden. |
Beispiel 1 ist so das, was man am Anfang der Delta-Drucker wohl am häufigsten gesehen hat: Auf Passung geschliffene Stahlwellen, auf denen Linearkugellager laufen. Das war default beim Rostock, dem Vorläufer vom Kossel, und funktioniert auch soweit. Es ist nicht das beste, oder tollste, oder genaueste Prinzip, aber es verrichtet seine Aufgabe recht zuverlässig. Auch hier kriegt man statt Kugellagern aus Stahl von Igus Kunststofflager, die dann eher Nadelspitzenlager sind. Hauptvorteil von Kunststofflagern: DEUTLICH weniger Geräuschkullisse, Metalllager sind einfach deutlich lauter auf den Wellen. Hauptnachteil: leider haben die Kunststofflager für die Wellen i.d.R. etwas zu viel Spiel, und das kostet Geschwindigkeit und Genauigkeit. Auch das gesamte Konzept hat leider einige Schwächen. Zum einen muss man natürlich seinen Wellendurchmesser am Rest des Druckers orientieren, will heissen, wenn der Drucker einen guten Meter hoch sein soll, kommtman mit den normalen 8mm-Wellen einfach nicht hin; das ist schlicht zu wackelig.
Die allermeisten Befestigungen des Schlittens an den Lagern werden darüber hinaus zumeist mit Kabelbindern gelöst. So oder so: Optimal ist das nicht. Leider habe ich einmal den Fehler gemacht, zwar geschliffene Wellen, aber nicht auf Passung geschliffene Wellen zu kaufen. Man glaubt kaum,was ein halber Zehntelmillimeter Spiel oder Unrundheit auf den Wellen anrichtet. Was ich relativ oft gesehen habe ist, dass Leute dem Problem damit versuchen beizukommen, dass man am Schlitten auf einer oder beiden Seiten zwei Lager übereinander montiert, um das auszugleichen, um eine längere „geführte“ Fläche zu haben, aber auch dass ist nur Flickschusterei, und bringt umterm Strich nicht das gewünschte Ergebnis.
Bei den normalen Verfahrgeschwindigkeiten kann sich hier dann schon ein „Springen“ der Lager auf den Wellen, oder ein Schleifen einstellen; mit der Gefahr, dass Lager klemmen, und Schrittverlust an den Motoren auftritt. Kunststofflager haben noch zusätzlich das Problem, dass – wenn sie zu fest mit Kabelbindern befestigt werden – leicht oval werden; ein schmaler Grat also. Das Laufgeräusch wird dadurch auch deutlich intensiver. Auch werden diese Gestängekonstruktionen mit zunehmender Länge der Wellen unzuverlässiger und „rappeliger“.
Beispiel 2: Linearführungsschienen. Das ist eigentlich das, was man haben will. Eine gehärtete Stahlschiene, die am Rahmen fest montiert wird, und ein Wagen, der mit einem gekapselten System umlaufender Kugeln darüber fährt (Achtung, der Wagen darf nicht von der Schiene entfernt werden, sonst fallen die Kugeln raus; die kriegt man auch nicht wieder rein ordentlich…). Nahezu spielfrei, leichtgängig, dadurch extrem hohe Beschleunigung und Geschwindigkeit möglich.
Auch die Positionier- und Wiederholgenauigkeit ist hier am besten. Diese Variante ist Standard beim „normalen“ Kossel Mini, und sieht darüber hinaus sehr professionell aus; und das nicht ohne Grund, denn Linearschienen sind auch in der Industrie der Standard für Konzepte wie diese, und können in fast alle Richtungen hohe Kräfte ohne funktionale Einschränkungen aufnehmen und ohne sich zu verformen. Verfahrgeschwindigkeiten von >350mm/s? Aber na klar! Einzig der Preis spricht gegen Linearschienen, denn selbst billige, mäßig gute Schienen vom „vertrauenswürdigen“ China-Seller auf Ebay kosten im Set von 3 Schienen von 400mm Länge plus 3 Wagen mit Versand etwa 100 Euro, Markenware entsprechend teurer. Da Linearschienen schon rein konzeptionell allen anderen Verfahren meiner Meinung nach überlegen sind, sind selbst billige Schienen meist gut genug für 3D-Drucker, generell gilt aber besonders bei Lagern: You’ll get what you pay for. Ordentliche Schienen sind halt teuer.
Lesson 7: Wenn schon sparen, dann nicht bei den Lagern.
Wie bei normalen Linearkugellagern auch, gibt es hier auch eine Alternative von Igus. Das ist ein Hersteller, der Lager aus einem speziellen Kunststoff herstellt, der nicht geschmiert werden muss, sich also auch für dreckige Einsatzumgebungen eignet, die sind dann aber noch teurer. Hauptvorteil von Igus-Schienen bei 3D-Druckern dürfte aber eher die deutlich reduzierte Geräuschkullisse sein.
Beispiel 3 „Fishing Line“ dürfte für die meisten ausscheiden. Das Prinzip ist, eine auf Rollen gewickelte Angelschnur statt eines Zahnriemens zu ziehen. Diese Rolle sowie die Umlenkrollen sind dann sogar druckbar, allerdings ist das ganze Konzept aus meiner Sicht eher ein Proof-of-Concept, es funktioniert, ja, aber bietet kaum Vorteile gegenüber anderen Konzepten, da die Angelschnur sowie deren Befestigung ein Limit setzt, was Beschleunigung und Verfahrgeschwindigkeit angeht.
Beispiel 4 beruht auf einem bestechend einfachem Prinzip. Ein Schlitten, nennen wir ihn mal „Wagen“ ist mittels 3 gummibereiften Kugellagern auf das Aluprofil des Rahmens „aufgeklemmt“. V-Slot heißt das deshalb, weil das Profil eine V-förmige Einsenkung in der Mitte hat, auf der der Wagen läuft. Das Konzept braucht zwar in der Höhe relativ viel Platz, ist aber einfach zu bauen (der Rahmen dafür kann z.B. gedruckt werden), braucht kaum teure Spezialteile und ist verhältnismäßig robust als Konzept. Spitzengeschwindigkeiten dürfen sich hier auch nicht erreichen lassen, aber sonst eine nette Alternative.
Den meisten Varianten (von den hier aufgezählten alle ausser „Fishing Line“) ist gemein, dass sie über einen Motor mit einem Ritzel einen Zahnriemen antreiben; entweder als Closed-Loop-Belt (wie beim Keilriemen, ein geschlossener Ring), oder halt als offener Riemen (dann werden die beide offenen Enden am Wagen fixiert). Auf der anderen Seite wird der Riemen (i.d.R. von einem Kugellager) wieder umgelenkt, und wieder in die Gegenrichtung zurückgeführt. Befestigt ist der Riemen nur am Wagen, sodass sich dieser mitbewegt, wenn der Motor den Riemen bewegt. In den meisten Fällen wird das relativ feine GT2-System für Ritzel und Riemen benutzt, aber dass ist erst einmal nur eine Kenngröße, die u.A. Größe und Abstand der Zähne beschreibt. Man kann auch andere nehmen, aber GT2 ist einfach und überall zu bekommen, und hat sich bewährt, und wie die meisten anderen Riemensysteme auch, haben GT2-Riemen (wenn man nicht den allerbilligsten nimmt) eine Stahl-Seele innendrin, sodass sie sich nach einer Initialphase in den ersten paar Wochen auch nicht weiter dehnen.
Best Practices
Es gibt das Ein oder Andere, was so kaum in irgendeiner Anleitung oder HowTo zu finden ist, aber vielleicht doch ein guter Tipp ist. Ich habe mal versucht ein paar solcher Dinge zusammenzutragen.
- Nutensteine
3D-Drucker werden in aller Regel mit Aluminiumprofilen für den groben Rahmenaufbau gebaut, meist sowas wie 20x20mm, T-Profil, Nut8 oder Nut5. Es gibt für fast jede Größe und Variante von Profil sog. Nutensteine. Das sind kleine, dreieckige oder flache Metallblöcke mit metrischem Gewinde in der Mitte, die man in die Nut der Profile einsetzt, damit man hinterher den Rahmen miteinander verschrauben kann, oder halt irgendwelche Addons anbringen kann (Display, Extruder, LED-Leisten, Lüfter, Filamentrollenhalter, you name it…).
Normalerweise hat man das nicht alles von vorn herein im Kopf, was man alles anbauen möchte. Und hinterher will man eigentlich auch nicht den Rahmen wieder komplett zerlegen, um da noch einen Nutenstein einzusetzten. Für genau diesen Zweck gibt es bessere Nutensteine, die man nachträglich in ein Profil einsetzten kann, ohne freien Zugang zu einem Ende des Profils zu haben. Diese kleinen, dreieckigen Metallblöcke sind grade so schmal, dass man sie in das Profil „einkippen“ kann, und haben auf der Rückseite eine kleine Stahlkugel, hinter der eine kleine Feder sitzt, welche die Kugel nach aussen drückt.
Dadurch bleibt der Nutenstein an der Stelle, an der man ihn eingesetzt hat, ist aber trotzdem verschiebbar. Diese Nutensteine sind zwar relativ teuer, und kosten etwa ~0.40€ pro Stück, aber ihr werdet diese Teile lieben. Auch wenn man für einen durchschnittlichen Delta schätzungsweise 50-70 Stück davon braucht, sind die Dinger jeden einzelnen Cent wert.
- Bowdenschläuche
Deltas haben normalerweise einen Bowden Extruder, das ColdEnd mit dem Motor ist also nicht direkt über dem HotEnd auf der Platform, sondern irgendwo Abseits am Rahmen montiert. Dazwischen ist ein Bowdenschlauch aus PTFE (besser bekannt unter einem seiner Handelsnamen: „Teflon“), der beidseitig mit Pushfits (Druckschlauchanschlüsse) befestigt ist.
Tipp 1:
Bowdenschlauch nicht zu lang lassen, nur so lang wie man ihn braucht. Denn je länger der Schlauch ist, je mehr Kraft muss der Motor aufwenden, um das Filament durchzuschieben, man muss ein relativ hohen Retract-Wert im Slicer einstellen, um Fadenbildung zu vermeiden.
Tipp 2:
Den Schlauch mit einem Kegelsenker oder etwas größerem Bohrer vorsichtig die Enden entgraten und einen kleinen Kegel reinsenken. Das Filament hat dann nicht nur weniger Widerstand beim durchgleiten, sondern lässt sich auch viel besser einfädeln im montiertem Zustand.
- Kalibrierung/Firmware
Tipp 1:
Die meisten Deltas werden wohl auf Marlin-Firmware laufen. Bei dieser gibt es ein paar Delta-spezifische Einstellungen; u.A. ein paar Offsets von der Mitte zum Rahmen, Platform Mitte zur Befestigung, usw… . Wenn man sich die Firmware etwas genauer anguckt, sieht man allerdings, dass viele dieser Werte hinterher einfach miteinander verrechnet werden. Bevor man also immer 10 Parameter gleichzeitig tuned, lieber einmal die korrekte Länge der Diagonalstäbe der Platform eintragen, und grob die anderen Werte eintragen, und dann hinterher nur einen der Werte, die verrechnet werden verändern. Grade wenn man kein Standardmaß beim Drucker hat, muss man hier sowieso experimentieren. Diese Werte beeinflussen im wesentlichen die Konvexität der Ebene. Man stelle sich vor, Dass das Druckbett, also quasi die Null-Ebene nur bei einem bestimmten Wert (den es herauszufinden gilt), eine Ebene ist. Darüber oder darunter wölbt sich die Druckfläche, sodass sie entweder konvex oder konkav ist (oder einfacher: eine Schüssel bzw. umgedrehte Schüssel statt einer Platte). Am einfachsten findet man das heraus, indem man seinen Druckkopf ~10mm oder so über das Druckbett fährt, und dann behutsam in Richtung Rand fährt. Je nach dem ob der Abstand vom Hotend zum Druckbett größer oder kleiner wird, je näher man an den Rand kommt, muss man den Wert entsprechend verkleinern oder vergrößern. Einfach mal zum testen den Wert mal großzügig in eine Richtung anpassen und vorher/nachher vergleichen. Lieber in diesen Punkt 1-2 Stunden extra Arbeit stecken, dann kann man sich auch so Addons wie „Auto-Bed-Leveling“ sparen, das braucht man dann nämlich nicht mehr, zumindest dann nicht, wenn man nicht auf eine Glasscheibe druckt. Das ist zwar alles relativ aufwendig, besonders, da man beim ersten Kalibrieren auch noch die Endstops gleich mitkalibrieren muss, aber es lohnt sich hier etwas mehr Arbeit zu investieren.
Tipp 2:
EEPROM beim Kalibrieren ausmachen und einmal Flushen. Wenn Ihr was kalibriert, und ihr euch wundert, warum sich keine Änderung einstellt, dann vermutlich, weil der entsprechende Wert in der Firmware durch den im EEPROM überschrieben wird. Erst wenn man fertig mit Kalibrieren ist, sollte man den EEPROM wieder anmachen in der Firmware und mit sinnvollen Werten füllen.
Tipp 3:
Baudrate auf 115200 statt auf 250000 setzten. Prinzipiell ist ja schneller besser, aber mal davon abgesehen, dass auch 115k-Baud völlig für die serielle Kommunikation mit dem Drucker reichen, gibt es technische Gründe: Grade das beliebte RepetierHost kann – zumindest auf Linux (auch unter Apple?! BSD??) – nur mit max. 115200 Baud umgehen, Grund dafür ist, dass RepetierHost mit Mono unter Linux läuft, und scheint ebendiese Limitierung für serielle Schnittstellen zu haben.
- Elektronik
Tipp 1:
Auch wenn viele anderslautende Meinungen dazu im Raum stehen: Gebt nicht 200+ Euronen für eure 32Bit-Elektronik und 128xMicrostepping Treiber am Drucker aus; Ganz im Ernst: Ein Ramps mit Arduino Mega 2560 (oder vergleichbar) ist mehr als ausreichend und vor allem spottbillig. Bevor ihr an die Grenze des Machbaren dieser Druckerelektronik kommt, gibt es viele viele Flaschenhälse, die vorher zum tragen kommen. Nur Steppermotor-Treiber kann man sich auch gerne für die DRV8825 entscheiden, statt den normalen Stepstick/Polulu, denn die DRV haben 32faches Microstepping, was dann doch smoother ist als 8x oder 16x. Ach ja, ein Display will man vielleicht noch, denn das zeigt nicht nur den Status zwischendurch an, sondern kommt auch oft (je nach Modell) gleich mit SD-Karten-Slot.
Tipp 2:
Pinout von den Endstops 3 mal kontrollieren. Der einfachste Weg, seine Elektronik zu grillen, ist den Endstop falsch draufzustecken. man zieht dann +5V VCC auf GND oder Signal und das wars dann in der Regel. Darum hier 3 mal hingucken, das ist mir schon mehr als einmal passiert. Ein Ramps hat die 5V-Leitung bei den Endstops mit daneben, weil man die für Endstops, die nicht einfach nur mechanische Schalter sind braucht. Oder z.B. weil die Endstop-Platine noch eine Status-LED mit dabei hat.
- Heizbett
Tipp 1:
Ich weiss wirklich nicht was alle Leute an Glasplatten zum Drucken so toll finden. Bei dem miserablen Wärmedurchgangskoeffizienten von Glas wundert es mich, dass PCB-Heatbeds überhaupt auf 100°C kommen können. Das ist pure Energieverschwendung. Gut, Glas ist in aller Regel sehr plan, jedenfalls mehr, als das meiste, was man sonst so kaufen kann, aber mittlerweile sind die PCB-Heatbeds so weit gereift, dass sie direkt auf eine 3 oder 4mm starke Aluminiumplatte gebonded (aufgebracht) sind. Einfacher gehts kaum. Schmeisst diese Glasplatten weg…
Tipp 2:
Eine Platte Kork (~3-4mm stark) direkt unter dem Heatbed angebracht, isoliert euren Drucker nach unten hin vor Hitze, wo i.d.R. die Elektronik sitzt; ausserdem geht der Stromverbrauch vom Bett runter, wenn nicht so viel Wärme nach unten verloren geht.
Tipp 3:
Ihr wollt euren Drucker beleuchten? Warum nicht 12V-LED-Stripes unters Heatbed kleben? Rote oder Orange LEDs, und einfach direkt an die Zuleitung des Heatbeds klemmen. Dann leuchten die nur, wenn das Bett heizt. Sieht hübsch aus, und ihr habt direkt optisches Feedback ob euer Heizbett an ist. Vorsicht jedoch bei den Lötsnschlüssen der Stripes: Wenn da Kontakt zum Heatbed besteht irgendwo, dann passiert zwar erst mal nichts, doch wenn dann die Düse des Hotends die Platte berührt, gibt es einen Kurzschluss. der Macht zwar weder dem Heatbed noch dem Hotend was aus, aber eure LEDs dürften schnell anfangen zu stinken; ausserdem grillt ihr damit in der Regel mindestens einen Thermistoranschluss an eurer Elektronik, und davon habt ihr in der Regel maximal 3, und braucht in meist mindestens 2! Also immer schön Schrumpfschlauch benutzen.
Tipp 4:
Bei der Kombination von Ramps und Heatbed: Lötet diese grünen Verbindungsstecker für den Stromanschluss vom Heatbed runter vom Ramps! Diese Konnektoren sind für 20A Spitzenströme ausgelegt. Wenn Ihr z.B. ABS druckt, und das Heatbed auf >=100°C peitscht, kann es passieren, dass diese Verbinder schmelzen (ist mir schon passiert, sogar bei 65°C schon), weil die Dauerlast z.T. schon auf über 20A klettert. Mit Glasplatte obendrüber potenziert sich dieses Problem im übrigen noch, denn Glas hat so den miserabelsten Wärmedurchgangskoeffizienten, den man an dieser Stelle überbaupt einsetzen kann.
Also besser Kabel mit ordentlichem Querschnitt (z.B. Kabelreste von Lautsprecherkabeln in ausreichendem Durchmesser) direkt anlöten und z.B. XT60-Stecker – wie sie im Modellbau üblich sind – als Verbinder benutzen. Die halten dann auch – wie der Name schon vermuten lässt – einer Nominal-Last von 60A stand. Besser als auf die (MOS)FETs vom Ramps zu vertrauen, ist meiner Meinung nach sowieso, ein DC-DC-Relais zu benutzen. Dann geht als einzig hohe Load der Strom vom Hotend und etwaiger Lüfter und LEDs durch das Ramps, und das sind für das Hotend normalerweise 40W-Kartuschen, also bei 12V weniger als 3.5A unter Volldampf. Die Hauptlast, also die, die durch das Heatbed erzeugt wird, geht dann durch das Relais. Dementsprechend gilt Lesson 8:
Ausreichenden Kabelquerschnitt auch bei Verbindern sicherstellen und 9:
Ein Relais am Heatbed macht das Leben leichter.
- Riemen
Tipp 1:
Man sollte nach ein paar Wochen die Riemen (egal ob GT2 oder T5 oder was auch immer) noch mal nachspannen, wenn sie neu waren, weil die sich initial noch mal etwas längen.
Tipp 2:
Auf Riemenspanner (diese Dinger, die aussehen, wie die Feder aus einer Wäscheklammer) sollte man besser verzichten. denn bei schnelleren Auf-/Ab-Bewegungen gibt der Spanner immer nur in einer Richtung nach, sodass Schlupf an der Umlenkrolle entsteht. Bei mir waren Drucke mit Spanner immer sehr viel unsauberer als ohne. Also besser per Hand Spannen die Riemen, und Lesson 10:
Keine Riemenspanner benutzen
… und zum Schluss dann noch mal zusammengefasst unsere Lessons Learned:
- Der erste Drucker den man baut, sollte ein Einfacher sein
- Gigantismus bei Deltas geht entweder mit Mehraufwand oder Qualitätseinbußen daher. Meistens beides.
- Nahe am „Standard“-Kossel zu bleiben, erspart viel Arbeit
- Für Deltas gilt: Verfahrgeschwindigkeit != Bewegungsgeschwindigkeit
- Auch beim Nachbau konstruktive Entscheidungen hinterfragen!
- Ein rundes, beheiztes Alu-PCB-Druckbett auf Federn ist besser als eine fest montierte Bor-Silikat-Scheibe
- Wenn schon sparen, dann nicht bei den Lagern
- Ausreichenden Kabelquerschnitt auch bei Verbindern sicherstellen
- Ein Relais am Heatbed macht das Leben leichter
- Keine Riemenspanner benutzen
Ich hoffe, das lesen dieses Artikel hat euch nicht so frustriert, wie mich das Lesen von Forenbeiträgen, wenn ich mal wieder irgendwas recherchieren muss. Ich habe bewusst auf Halbwahrheiten und Hörensagen verzichtet, denn das bringt keinen weiter. Ich habe die Sachen, die ich einfach nur besser finde als andere, wo es auch noch valide andere Ansätze gibt, auch als solche gekennzeichnet, aber schlussendlich muss sich ja eh jeder selbst ein Bild machen. Dies hier sind zumindest meine Erfahrungen. Mögen sie euch hilfreich sein.
Ein Update zur Softwareseite bzw. zum Drucken selbst kommt dann demnächst mal.
Bleibt nur zu sagen: Happy Printing!
-zeus
Sehr interessant und hilfreich, da wir im Moment dabei sind, einen Delta zu bauen mit d=600 und h=1000 (!). Wenn das mal gut geht……..
Sind gespannt auf den Bericht über Software! Wann kann man damit rechnen?
E. & P.
Uff, also ich habe das Projekt zugunsten Anderer mal als Winterprojekt vertagt. Ich hatte, wie bereits erwähnt, ja schon mal zwei deltas, die sehr vergleichbar waren gebaut. einen mit h=~800 und einen mit h=1000 (Gesamthöhe, nicht effektive Druckhöhe). Unterm Strich kann ich nur davor warnen, einen Drucker mit einem Meter Höhe zu bauen, es sei denn man macht sich wirklich ausreichend Gedanken über den Aufbau. Zum einen schiessen die Kosten nicht-linear in die Höhe, wenn man auf einmal alle Teile in „eine Stufe besser“ braucht, weil man die z.T. einfach nicht so leicht bekommt, und zum Anderen sollte man sich wirklich fragen, ob man einen Delta dieser Höhe wirklich braucht. Das Für und Wider habe ich ja eigentlich hinreichend dargelegt. Natürlich sind bei Deinem/Ihrem Bauvorhaben bei d=600 die Proportionen wieder deutlich „natürlicher“, als bei den meisten hohen Deltas, die einfach nur weiter in die Höhe gehen, aber man sollte sich auch vor Augen halten, dass man statt einem Drucker mit h=1000 und d=600 auch zwei Drucker mit h=500-600 und d=250-350 bauen kann, was den Aufwand in Zeit und Geld angeht.
Einen Abriss über die Software – sowohl auf dem Drucker als auch auf dem Rechner – und die Stolpersteine, die Einem hier eventuell begegnen, habe ich nach wie vor vor (komisches Satzkonstrukt), und auch wenn ich 2/3 des Artikels auch mehr oder weniger aus dem Kopf schreiben könnte, macht es doch mehr Sinn, das parallel beim Aufbau und Setup eines Druckers zu erledigen. Ich habe letztes Jahr einen „Sparkcube“-artigen Drucker gebaut (also vom Prinzip her ein CoreXY-Drucker), der auch gut funktioniert, und habe mich dann dazu entschlossen, meinen Delta zu zerpflücken, und den in etwas konservativeren Ausmaßen neu aufzubauen. die Hardware ist zwar schon soweit fertig aud aufgebaut (naja, zu 90% etwa…), aber wie gesagt, das habe ich als Winterprojekt vertagt. solange das Wetter noch mehr oder minder mitspielt, versuche ich mich wieder etwas mehr der Analogen Schwarz/Weiß-Fotografie zu widmen. Aber da kommt auf jeden Fall noch ein Artikel zur Software.
Gruß,
-zeus-
Pingback: Keramik 3D Drucker – Saarbastler